X.
The Trials and Tribulations of Creating a Smart Textile
The Trials and Tribulations of Creating a Smart Textile
Jake Tan Jun Kang Nanyang Technological University, Singapore jtan325@e.ntu.edu.sg |
Galina Mihaleva Nanyang Technological University, Singapore gmihaleva@ntu.edu.sg |
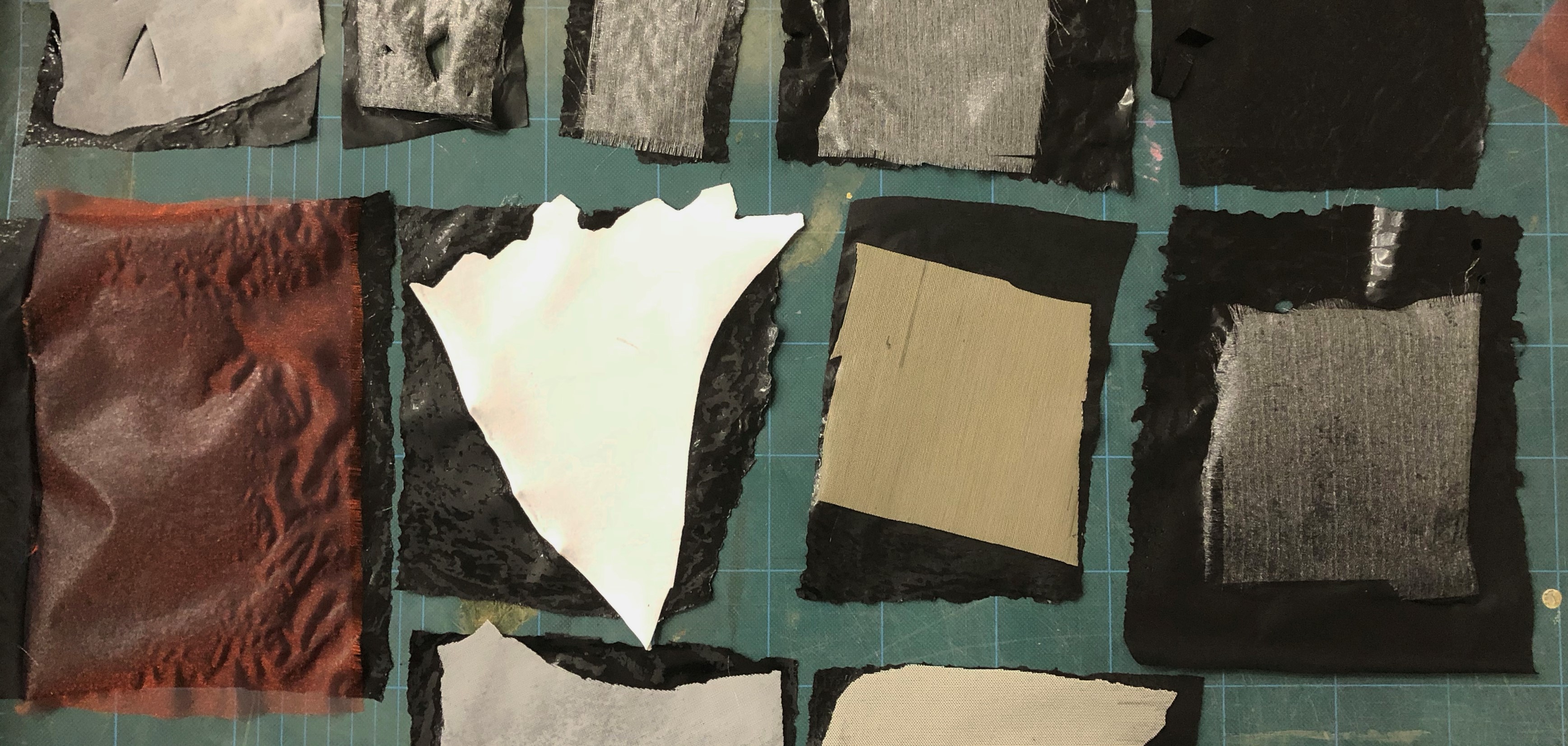
(Figure 1: Experimentations of Composite Fabrics and LDPE)
ABSTRACT
This is a debrief on the conceptualisation, processes and outcomes of developing a smart textile. As an artist and programmer, I am always finding ways to create and control systems, be it microcontrollers, games, networks, projection mapping or 3D printed mechanisms. As an intersection to sciences, I sought to understand if there were natural elements and materials that could be altered and fused to create composites that could actuate under certain parametric conditions. The design and experimentation process of obtaining this naturally moving material would be heavily influenced by artistic and scientific research methodologies. The plan would be to introduce these programmable actuating materials onto garments.
I would like to preface that the experimentations conducted did not succeed in naturally actuating the compounded materials at resting room temperature.
1 RELEVANT LITERATURE
As a form of study, I was heavily inspired by the work done at MIT, in particular, their Media Lab department. Neri Oxman, Hiroshi Ishii and Pattie Maes were big inspirations for myself because their research goals aligned with mine. Oxman’s Silk Pavilion(2013) and Minotaur Head with Lamella(2012) were innovative ideas on generative biomimetics aspects of naturally occuring yet programmable processes. Oxman’s research at Mediated Matter used technology to fabricate, and predict natural behaviour; creating accurate datasets. In unison, the process achieves a symbiosis between nature, environment, humanity and machines. With an emphasis on material ecology, most of the work behind Mediated Matter ends up being analogous upon appearance but drastically boundary breaking because of how and what it is made of.
Ishii’s Tangible Media group gave birth to the bioLogic(2015), a living and actuating garment that harnesses the power of bacteria as natural actuators from their contraction and expansion due to humidity. The work attempts “to program living organisms and invent responsive and transformational interfaces of the future.” Through fusing carefully selected fabrics with structurally engineered natto cell bacteria, the team was able to create natural actuators that utilized heat and humidity given off naturally by the human body as a means of energy to power the actuation.
(Figure 2: Active Textile exhibited at Cooper Hewitt Museum)
Maes’ iconic Fluid Interfaces works such as DermalAbyss(2017) and Argus(2019) have inspired how I view technology, art and design. But an important work that was discovered during my literature research was, coincidentally, another work from MIT, but from their Architectural department, specifically their Self-Assembly Lab led by Skylar Tibbits. Their focus is mainly on creating programmable materials that can self assemble and actuate under circumstances. One of their smaller works stood out as something viable and worth experimenting and recreating. Active Textile, a series of works produced by the lab, encompasses the idea of fusing complimentary materials that generate controlled actuation based on environmental or external stimulus. The series works with fashion brands across the globe and have produced shoes and garments through the experimentation process. For me, I was particularly interested in the efforts of fusing plastics and fabrics in their early prototypes of the series.
2 METHODOLOGY
In an effort to mix biomimetics and interfaceable wearables, I landed in the conclusion of an approach to a non-technological, programmable, adaptable input output wearable. Moving forward, heavily inspired by the materials used in the first version of Active Textile, I set out to investigate the materials and methods used to create the compound.
The idea would be to try to replicate their processes and materials before proceeding to innovate on my own iteration. In an interview with Popsci, Tibbits reveals that there are 6 layers behind Active Textile of which actuation occurs due to the fusion of two different coefficient thermal expansion materials that would have not actuated without the compounding process.[Cummins 2018] The only material revealed was a low density polyethylene(LDPE), a common plastic known primarily for its strength, durability and ability to heat shrink as a film[American Plastics Council 1996], of which would be laminated onto an unknown fabric[Tibbits, 2016].
Through this, the experimentation had only one constant: the low density polyethylene film. The two variables that were unclear would be duration of lamentation and type of fabric. Acquiring different fabrics of varying properties for testing would ensure the highest success rate of finding out the hidden variable. Upon experimentation with a fabric hot iron, there seemed to be inconsistencies with the applied heat. Understandably, that must have been the reason a lamination machine was used. Replacing the lamination machine would be a hot iron heat press that would be used at different durations. The temperature remained as a constant of 140 degrees as to keep in line with most traditional lamination machines and to graze the melting point of the LDPE, making it permeable for fusion.
The fabrics used:
- A variety of Organzas
- Netting
- Lycra Spandex
- Nylon
- Standard Cottons
3 MATERIALITY
The materials chosen for experimentation were mainly extremities of their strengths as a fabric. Important details to note that were discovered during the experimentation process was that light weight fabrics such as organza and nylon tend to curl inwards to the fabric. A weighted fixture was placed upon the fabrics to create a flat, resting position as it cools. This behaviour is clearly exhibited when slits were cut at room and at heated temperatures. However, none of the slits in the fabrics ever recovered to their resting positions.
Multiple different types of organzas were used mainly due to the fact that varying organzas have different purities that could affect its ability to fuse with plastics. Their unique polyester based material means they are also part of the polyethylene family of synthetic materials. The unique differences between polyester organzas and LDPE are mainly it’s melting points; LDPE sits at 105°C to 115°C, and organza at 295°C. The materials bond well when heated above the melting point of LDPE and given ample time for it to fuse and cool. Upon too much heat and prolonged time in the hot press, the LDPE exhibits an overburnt, almost crispy texture that is not as flexible and flimsy as the optimal 140 degrees at 180 seconds. Even cutting slits in the compound would cause the material to curl inwards, but never recovering back to its initial position. Concluding that the fabric did not have enough actuating potential to pull the contracting LDPE back.
Throughout, we experimented with various organza such as a red Organdy that has a combed fibers to organza’s twisted fibers, along with an already heat molded polyester based organza. Including the nylon, cotton and netting, none have returned results that were significantly different from ordinary polyester based organza as none of the slits would return to their resting positions. There were attempts to use a fabric iron to induce enough heat in the effort of expanding the plastic so the slits would return to resting positions.
Lycra Spandex being one of the stretchiest fabrics should have yielded a different result. Melting at 450 degrees and with a much tougher tensility succumbing to the parameters of its counterpart. Similar to the rest of the results, the contraction of the LDPE would cause the fabric to curl inwards of the LDPE along with it’s slits that do not recover as well.
4 CONCLUSION
A bulk of the research came from understanding the LDPE and its properties. The fabric was never a main concern for the project as it seemed like a plain weave. But as one half of the equation, it soon came to light how important it was to have studied the thermal expansion properties of each fabric before attempting the experimentation.
The expanding CoVid-19 Pandemic, fabric and supplies have been forced to close down and facilities to continue experimentation have been locked down.
Moving forward, more research will be conducted about the thermal expansion properties of fabrics by going into detail their Linear Coefficient of Thermal Expansion. Minute details such as micro-stress as a parameter to thermal expansivities[Sideridis 1994] would also play a role in the final selection.
The slitted material will be used in garments that can assist construction workers. The material will be located where air flow and perspiration are concentrated. This regulates temperatures; dorso teres major, posterior triceps, posterior forearm and anterior wrist.
The practical use of this compression uniform will serve to lower internal bodily temperatures, integrate high visibility safety features, body odour reduction and stylistic look.
The practical use of this compression uniform will serve to lower internal bodily temperatures, integrate high visibility safety features, body odour reduction and stylistic look.
REFERENCES
E. Cummins, This textile's twitching tendrils hint at a future of programmable materials, Popular Science, July 18, 2018, https://www.popsci.com/programmable-materials-living-wall/
American Plastics Council, UNDERSTANDING PLASTIC FILM: Its Uses, Benefits and Waste Management Options, December 1996
S. Tibbits, Active Self-Transformable Textiles, US 2016/0340826 A1, United States Patent and Trademark Office, 24 November 2016.
E. Sideridis, Thermal expansion coefficients of fiber composites defined by the concept of the interphase, Composites Science and Technology, Volume 51, Issue 3, 1994, Pages 301-317, ISSN 0266-3538, https://doi.org/10.1016/0266-3538(94)90100-7. (http://www.sciencedirect.com/science/article/pii/0266353894901007)
AUDIOVISUAL
(Video 1: A summary of the processes of experimentation)
(Video 2: Initial Experimentations with Lycra Spandex with a Fabric Iron)
(Video 3: Experimentations with Lycra Spandex and cooling down effects)
(Video 4: Using Hot Air Gun on Lycra Spandex to encourage actuation with heat)